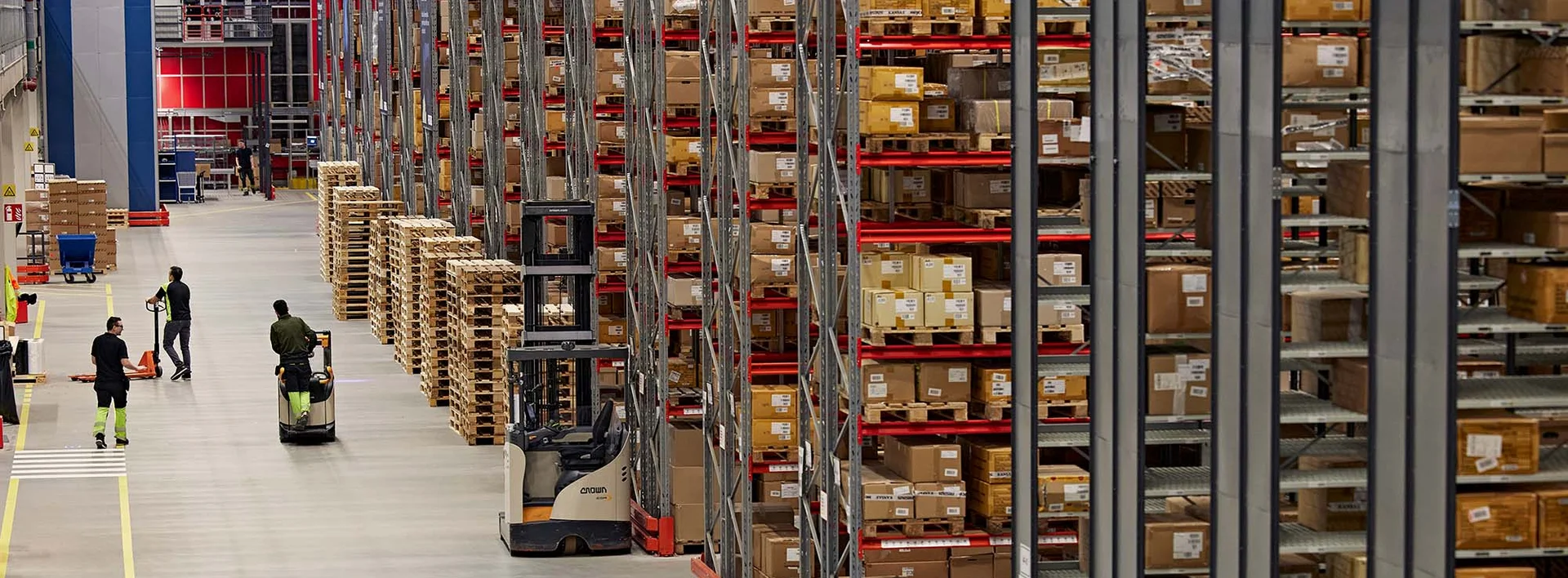
social compliance
We recognise that our business has an impact on environmental and social aspects far beyond our own immediate operations and we work with long-term suppliers that share the same values.
Since 2016, we are part of amfori BSCI, the leading supply chain management system that helps companies work with assessing and improving social and environmental standards in their supply chain. By joining forces with amfori BSCI we aim to guarantee ethical working conditions for all workers in our supply chain. The amfori BSCI organisation follows the ILO core conventions and the UN Global Compact
1. Risk assessment
All potential Fristads suppliers go through a risk assessment before being onboarded. The risk related to governance in sourcing countries is based on the Worldwide Governance Indicators from the World Bank. The countries’ risk level is assessed in six areas and depending on how they score, countries are classified as either ‘low risk’ or ‘high risk’.
2. Onboarding
New suppliers must fill out a self-assessment form, complete a questionnaire on the Worldfavor platform and sign Fristads’ Code of Conduct and Restricted Substances List (RSL). Additionally, new suppliers must demonstrate that they comply with the requirements in Fristads’ Code of Conduct by conducting a third-party audit. The commitment to the Code of Conduct and the RSL must be renewed annually.
3. Ongoing support and training
Fristads’ CSR team works closely with our quality control team to monitor suppliers’ compliance during the production of Fristads orders. We have also developed a new training program for our sourcing associates and approved suppliers, to ensure that they are up to date on forthcoming EU due diligence regulations.
4. Third-party factory audits
To ensure that our suppliers live up to our requirements, we audit factories against the amfori BSCI and other established standards through mandatory third-party audits. Fristads’ suppliers can be audited at any time, but typically every or every other year. Occasionally, we send an auditor to the approved suppliers to carry out enhanced due diligence to ensure suppliers’ compliance in case of any noncompliance issues reported.
5. Remediation plans and follow-up
Deviations that occur during a factory inspection must be corrected through a remediation plan and followed up with a new audit or desktop review. The purpose of the remediation plans is to constantly improve working conditions and environmental standards at the factories. If the corrective steps are not followed promptly, we will terminate our business relationship with the supplier.
Fristads is a signatory to the International Accord on Health and Safety in the Garment and Textile Industry, furthering our commitment to the original 2018 Bangladesh Accord. Through the agreement, Fristads commits to the health and safety work already undertaken in Bangladesh and to the expansion of the principles to other countries. All our suppliers are required to have undergone Accord remediation.
More content for you:
Stritex, our factory located in Ukraine, has been in business for 70 years. Since 2001, the factory has produced high-quality workwear and flame-retardant products for Fristads.
High-quality products and long-term partnerships are closely connected. Our suppliers are thoroughly screened to ensure that they meet our requirements.
At our office in Hongkong, professionals from all over the world work together to improve the operation and quality of the products, and ensure good working environments.