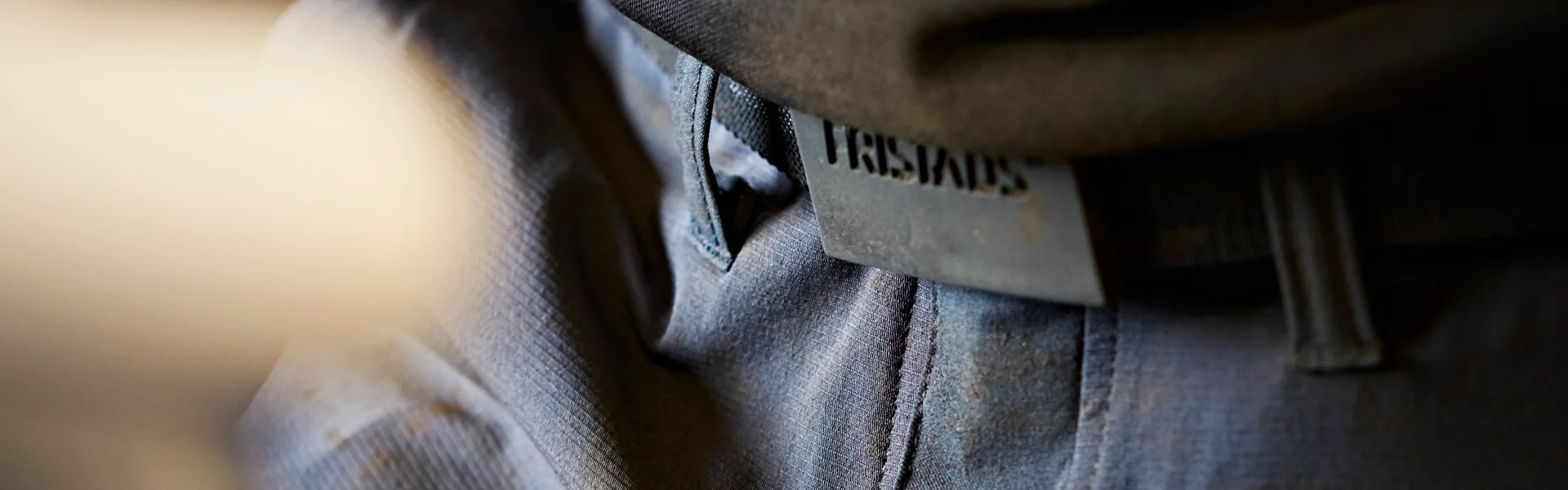
Circular product cycle
USING A LIFECYCLE PERSPECTIVE
At Fristads, we use a Life Cycle Assessment (LCA) to help us determine areas that can be improved from a sustainability perspective. For every new garment that is produced, we consider the impact it has on the environment and what we can do to minimise the negative effects. All Fristads departments are guided by the LCA, as it provides the framework for our environmental work. Our LCA includes six areas: Design, Material and production, Facilities, Transports, Users and Close the loop.
Fristads’ design department is tasked with making every new product a little more sustainable than the last one. To reach that goal, they are leveraging innovative technology and embracing new ways to work. For example, the design department is facilitating Fristads’ transition to more sustainable materials, by making the sustainable choice the default when the technicians “build” a garment. Other initiatives include designing garments with re-use and recycling in mind, and finding creative ways to make use of materials that are leftover, are already in stock or have been used for discontinued products. Leftover materials are regularly incorporated in new products and used to create limited collections of a few hundred garments.
We carefully choose the materials and trims for our workwear based on the performance, durability and environmental impact of the finished garment. As a part of our environmental work we are exchanging the materials in our collections for more sustainable alternatives on an ongoing basis and develop customised, more sustainable collections for several of our larger customers. Aside from yarn and fabrics, we also use materials like cardboard and plastics for our packaging. Two of our strategic goals are to minimise the amount of packaging materials that are used and to use more sustainable materials whenever possible for the packaging that can’t be eliminated.
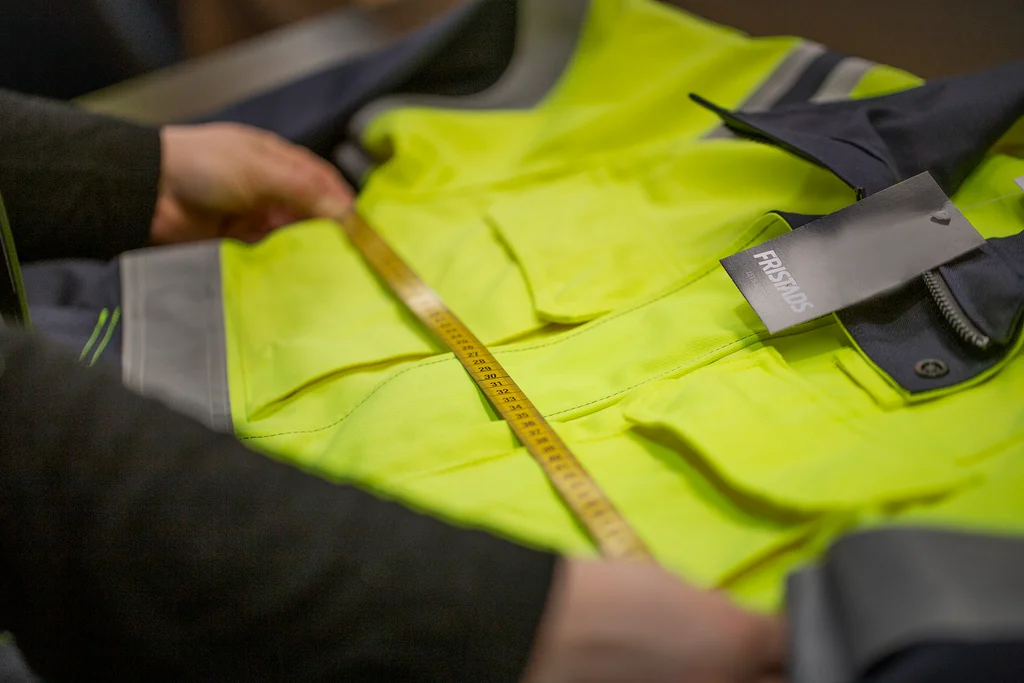
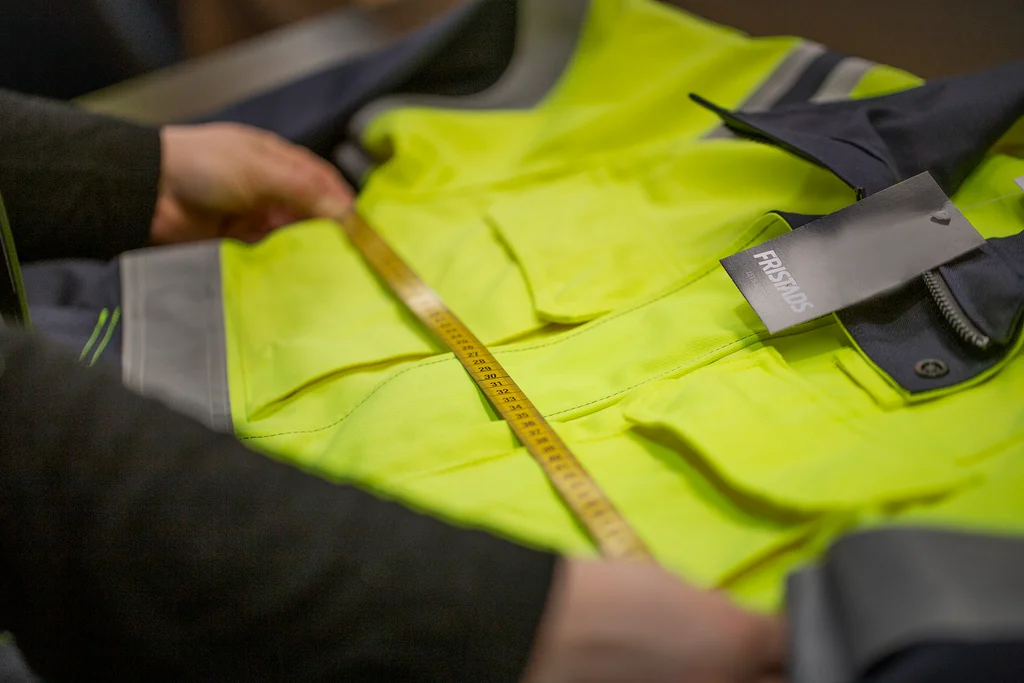
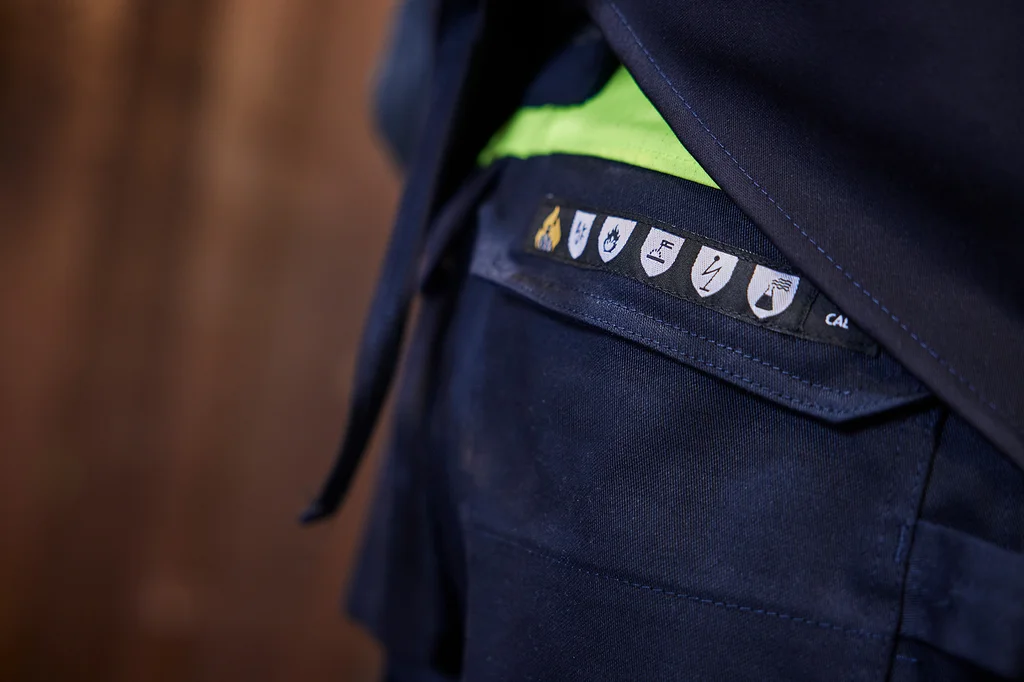
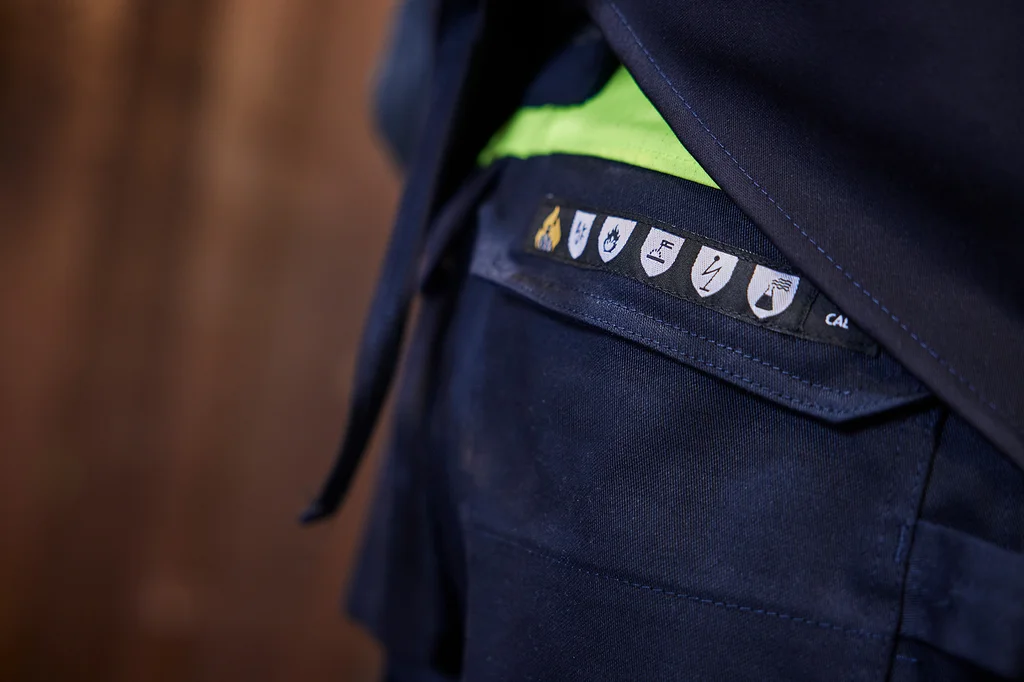
The greenhouse gas emissions that can be traced to Fristads’ own operations and facilities only make up a small share of our total environmental footprint. Still, we are continuously working on reducing fuel and electricity consumption in our own facilities, for example by monitoring and optimising the energy use at our headquarters in Borås, Sweden. Our goal is to increase the share of electricity from renewable sources in our own facilities from 97 percent to 100 percent, as well as increasing the share of the total energy use that is covered by renewable energy certificates, from the current level of 50 percent.
To minimise emissions, we strive to ship most of the products that are made at our partner factories in Asia and Africa with ocean freight and only use air transports when there is no other option. We work closely with both garment producers and freight carriers to optimise the containers we ship and try to avoid partial loads. We also consolidate goods from our European producers to optimise transport volumes on land. Since 2019 Fristads participates in a research and development project on so-called High-Capacity Transports to make road transports from the port of Gothenburg to the warehouse in Borås more efficient.
We aim to make it easier for our users to make conscious choices about their workwear purchases. One way we do this is by developing environmentally declared workwear collections, where the garments have been analysed from a sustainability perspective, from the choice of design to the delivery of the finished product to our warehouse. From the start, our goal has been to offer environmentally declared garments in every product category, so that all workers will be able to dress sustainably, regardless of their profession. So far, we have produced Fristads Green garments for craftsmen and the service and industry sector, as well our high-vis and cold, wind and rain product segments.
More content for you:
To reduce the environmental impact connected to our operation we have initiated a number of activities to promote a sustainable development.
Read more >
We carefully choose the materials and fabrics for our workwear based on the performance, durability and environmental impact of the finished garment.
Read more >
The Environmental Product Declaration (EPD) is a tool that guides customers, buyers and those responsible for public procurement to making more insightful decisions.